Brochure
Download our document to see specific data of the service and how we work.
Let’s Start Work
Together
Please feel free to contact us. We will get back to you with 1-2 business days. Or just call us now.
377 villa, dream city, Erbil, Kurdistan region of Iraq
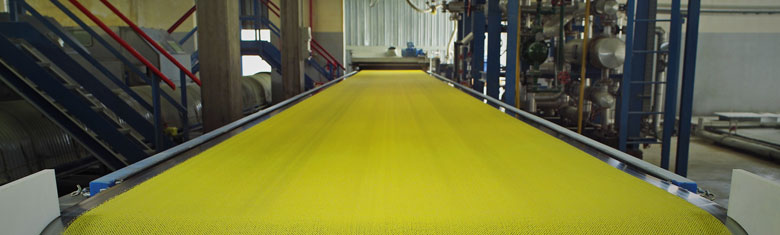
Production of Sulphur carried out in three basic ways:
- Mined through the use of wells drilled to sulphur deposits and worked with the “Frasch” method;
- Extracted from the oil or gas stream at a processing plant;
- Scraped from the surface of the earth or dug out of open pits.
“Crude” sulfur is produced from the Frasch process or recovered from “sour” natural gas or petroleum. Although termed “crude”, this sulfur possesses a minimum purity of 99.5 percent and is suitable for a majority of uses. The impurities consist primarily of trapped organic matter.
Sulphur recovery from the Mines
In some regions of the world the sulfur occurs at depths of 500 to 3,000 feet in domes subterraneously up-thrust by columns of salt. This native sulfur associated with the caprock of salt domes and in sedimentary deposits was mined by the Frasch hot-water method, in which the native sulfur was melted underground and brought to the surface by compressed air. The Frasch process utilizes a steel tube made up of three concentric pipes that are driven underground to reach the sulfur deposit. Superheated water is then pumped down under great pressure in the outermost pipe to melt the sulfur. Air pressure from the innermost pipe forces the sulfur up the third pipe to the surface where it cools and solidifies.
In 1900, Herman Frasch was trying to perfect his hot water melting process for producing sulfur. Domestic production was about 3,200 metric tons of sulfur valued at $88,100. Native sulfur deposits in Louisiana, Nevada, Texas, and Utah were mined with conventional mining methods. Domestic sulfur production, including mined elemental sulfur and pyrites, supplied about one-quarter of the U.S. sulfur demand of about 415,000 tons. Most sulfur and pyrites, domestic and imported, were used to produce sulfuric acid that was consumed in many different industries. Virtually all elemental sulfur imports came from the Italian island of Sicily, and pyrite imports were from unspecified locations. Pyrites remained a significant raw material for sulfuric acid until 1982. When the Frasch process was successfully commercialized in 1903, the U.S. sulfur industry took a turn for the better. By about 1915, the United States surpassed Italy as the world’s leading producer of sulfur, a situation that continued throughout the century, during which eight companies produced nearly 340 million tons of sulfur from 36 mines in Louisiana and Texas. Frasch sulfur production hit its peak in 1974 when 12 mines produced 8 million tons.
Recovered Sulphur from oil or gas
Recovered elemental sulfur, a nondiscretionary byproduct from petroleum refining, natural gas processing, and coking plants, was produced primarily to comply with environmental regulations that were applicable directly to emissions from the processing facility or indirectly by restricting the sulfur content of the fuels sold or used by the facility.
Recovered sulfur tonnages are expected to increase as the demand for clean-emission fuel continues.
Sulfur recovery refers to the conversion of hydrogen sulfide (H2S) to elemental sulfur. Hydrogen sulfide is a byproduct of processing natural gas and refining high-sulfur crude oils. The most common conversion method used is the Claus process. Approximately 90 to 95 percent of recovered sulfur is produced by the Claus process. The Claus process typically recovers 95 to 97 percent of the hydrogen sulfide feedstream.
Sulfur removal facilities are located at the majority of oil and gas processing facilities throughout the world. The sulfur recovery unit does not make a profit for the operator but it is an essential processing step to allow the overall facility to operate as the discharge of sulfur compounds to the atmosphere is severely restricted by environmental regulations. Oil and gas producers are attempting to maximise production at minimum cost. This often means debottlenecking existing upstream facilities and may result in extra sulfur recovery capacity being required. Oil refiners are also increasingly being forced to comply with legislation reducing the levels of sulfur in products. Combine this with the ability or need to process sourer crude oils and many refiners find that their existing sulfur recovery units do not have sufficient capacity. Furthermore, in many countries environmental legislation is demanding higher recoveries from sulfur recovery units.
Crude natural gas recovered from wells contains fairly high concentrations of H2S and SO2 gases that are separated and converted to elemental sulfur in gas processing companies via different processes (usually Claus process). This process is called gas sweetening process. Condensations or petroleum cuts also could contain sulfur compounds (e.g. mercaptans) that are separated via various processes and are converted to elemental sulfur. According to the industrial reports, more than 45% and 48% of global sulfur is produced in petroleum and gas industries, respectively.
The main uses of Sulphur
- The main use of sulphur is in the preparation of SO2 which is used in the manufacture of sulphuric acid.
- Sulphur is used in the manufacture of carbon disulphate, sodium thiosulphate, gun powder, matches and in fireworks.
- Sulphur is used on vulcanization of rubber. Natural rubber is soft and sticky. Heating it with sulphur makes it hard non-sticky and more elastic. This process of heating of natural rubber with sulphur is known as vulcanization.
- Sulphur is used as fungicide and insecticide in agriculture and as a disinfectant in medicines.
- Sulphur is used in ointments for curing skin diseases.
- Sulphur is used in beauty parlours to give specific shapes to the hair.