Brochure
Download our document to see specific data of the service and how we work.
Let’s Start Work
Together
Please feel free to contact us. We will get back to you with 1-2 business days. Or just call us now.
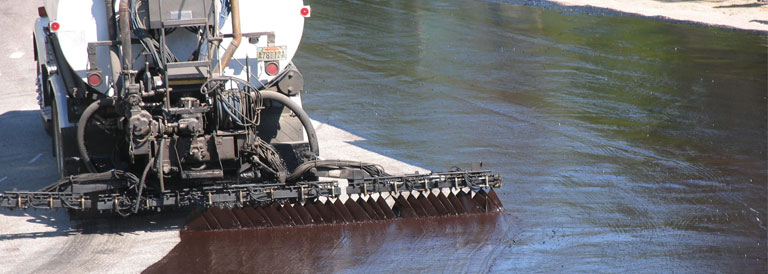
Bitumen emulsions are usually dispersions of minute droplets of bitumen in water and are examples of oil-in-water emulsions.
The bitumen content can be varied to suit different requirements and is typically between 30% and 70%. The primary objective of emulsifying bitumen is to obtain a product that can be used without the heating normally required when using cutbacks and paving grade bitumen.
In the manufacture of bitumen emulsions, hot bitumen is sheared rapidly in water containing an emulsifying chemical (emulsifier). This produces very small particles of bitumen (the dispersed phase) dispersed in water (the continuous phase). The bitumen particles are stabilised in suspension and do not readily coalesce due to the presence of the emulsifier, which is concentrated on the surface of the bitumen particles.
During application, the water in a bitumen emulsion is either lost by evaporation, or it may separate from the bitumen because of the chemical nature of the surface to which the emulsion is applied. This process is referred to as breaking. Because bitumen has a density only slightly higher than water, sedimentation of the bitumen droplets in an emulsion during storage is very slow. Emulsions can usually be regenerated after long storage times by gentle stirring to redisperse the bitumen droplets.
Types of Bitumen Emulsions
Bitumen emulsions are available in many different forms, either cationic or anionic, with varying breaking or setting rates and binder types and contents.
The two most common basic emulsion types are designated by the letter ‘C’ for cationic emulsions, as in CRS (cationic rapid setting), and by the letter ‘A’ in anionic emulsions, as in ASS (anionic slow setting).
Cationic Bitumen Emulsion
When the emulsion is being produced the cations are adsorbed by bitumen droplets, negatively ions remain in the water. The undeniably most complete field of use is represented by the rapid setting emulsions.
Anionic Bitumen Emulsion
Most often, fatty acid and resin acid alkaline salts are used. They are obtained by saponification of the liquid resin, called Tall-Oil. This substance is a residual, distilled substance, a by-product of the paper pulp industry from resinous wood treated using the “sulfate” process.
The Co2Na group is the hydrophilic polar part. When in a solution in the continuous aqueous phase, the soap molecules become ionized; the Na (or K) ions are the cations adsorbed by the water and the rest of the molecules are the anions adsorbed by the bitumen globules.
The characteristics of an emulsion are designated by the terms rapid (R), medium (M) and slow (S). The main grades for bitumen emulsions are classified as follows:
Cationic Emulsions | Anionic Emulsions | |||||||
---|---|---|---|---|---|---|---|---|
Rapid Settings (RS) Type | CRS-1 | CRS-2 | RS-1 | RS-2 | ||||
Medium Settings (MS) Type | CMS-2 | MS-2 | ||||||
Slow Settings (SS) Type | CSS-1 | CSS-1h | Modified CSS-1h | SS-1 | SS-1h | Modified SS-1h |
Slow setting emulsions are more stable than medium setting emulsions which, in turn, are more stable than rapid setting emulsions.
Cationic vs Anionic
The coating of the bitumen particles by the emulsifier gives them an electrostatic charge. Depending on the type of emulsifier, this can generally be either negative or positive. The interaction of the charged particles is the reason it is possible to make emulsions that do not rapidly revert to the separate phases.
Emulsions in which the bitumen droplets are negatively charged are called anionic emulsions. Emulsions in which the particles are positively charged are called cationic emulsions.
To ensure that an emulsion remains either anionic or cationic, its pH (that is the balance of acids and bases) is controlled so that typically an anionic emulsion has an alkaline pH of over 7 and a cationic emulsion has an acidic pH of below 7.
This fundamental property of both anionic and cationic emulsions requires that they never be mixed. Mixing of an anionic emulsion and a cationic emulsion allows the negatively charged anionic bitumen emulsion droplets and the positively charged cationic bitumen emulsion particles to come together through electrical attraction. Ultimately enough droplets will combine and the bitumen will separate out, becoming unusable and destroying the emulsion.
Applications of Bitumen Emulsions in Bituminous (asphalt) Pavement Construction and Maintenance:
TACK COAT: Tack coat (also known as bond coat) is a light application of asphalt emulsion between hot mix asphalt layers designed to create a strong adhesive bond without slippage. Heavier applications may be used under porous layers or around patches where it also functions as a seal coat. Without tack coat the asphalt layers in a road way may separate which reduces the structural integrity of the road and may also allow water to penetrate the structure. The type of emulsion used for tack coats varies from country to country. Normal practice in the USA is to use a slow-setting emulsion that is diluted with water before application. In many European countries cationic rapid setting or specially designated low viscosity medium setting emulsions are used, which are applied undiluted.
PRIME COAT: Prime coats protect the integrity of the granular base during construction and help reduce dust. In the case of a base which is to be covered with a thin hot mix layer or a chip seal for a low volume roadway, priming ensures a good bond between the seal and the underlying surface which otherwise would have a tendency to delaminate. Compared to cut back asphalt primes, emulsion primes are environmentally friendlier. Slow-setting grades of asphalt emulsions (diluted with water before application) are suitable. With dense granular bases, or stabilized bases the surface may need to be broken up by scarifying before application, to ensure good penetration.
Cationic Emulsified Bitumen Specification (AASHTO M208, ASTM D2397)
Type | Rapid-Setting | Medium-Setting | Slow-Setting | |||||||
---|---|---|---|---|---|---|---|---|---|---|
Grade | CRS-1 | CRS-2 | CMS-2 | CSS-1 | CSS-1h | |||||
Min | Max | Min | Max | Min | Max | Min | Max | Min | Max | |
Test on emulsions: | ||||||||||
Viscosity, Saybolt Furol at 25°C SFS | 20 | 100 | 20 | 100 | ||||||
Viscosity, Saybolt Furol at 50°C | 20 | 100 | 100 | 400 | 50 | 450 | ||||
Storage stability test, 24-h, %B | 1 | 1 | 1 | 1 | 1 | |||||
Demulsibility, 35 mL, 0.8% dioctyl sodium sulfosuccinate,% | 40 | … | 40 | … | ||||||
Coating ability and water resistance: | ||||||||||
Coating, dry aggregate Coating, after spraying Coating, wet aggregate | good fair fair | |||||||||
Coating, after spraying | fair | |||||||||
Particle charge test | positive | positive | positive | positive | positive | |||||
Sieve test,%B | 0.10 | 0.10 | 0.10 | 0.10 | 0.10 | |||||
Cement mixing test,% | 2.0 | 2.0 | ||||||||
Distillation: | ||||||||||
Oil distillate, by volume of emulsion,% | 3 | 3 | 12 | |||||||
Residue,% | 60 | 65 | 65 | 57 | 57 | |||||
Tests on residue from distillation test: | ||||||||||
Penetration, 25°C, 100g, 5s | 100 | 250 | 100 | 250 | 100 | 250 | 100 | 250 | 40 | 90 |
Ductility, 25°C, 5 cm/min, cm | 40 | 40 | 40 | 40 | 40 | |||||
Solubility in trichloroethylene, % | 97.5 | 97.5 | 97.5 | 97.5 | 97.5 |